Optimisation of visual inspection process
Application Track:
Code:
Domain:
Proposed by:
Entity Logo:
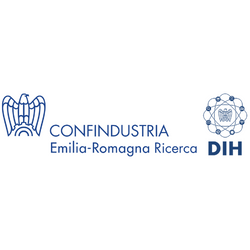
Summary of the entity:
CERR mission is to support companies, in particular SMEs, in their journey to innovation, both incremental and disruptive innovation, with a special focus on digital transformation, AI and HPC. CERR has developed an integrated approach to service mixing access to finance, technology and innovation match-making with training and supporting activities in the adoption of enabling technologies, with a focus on Industry 4.0. CERR promotes collaboration, dissemination of ideas and the exploitation of knowledge to experiment and find new ways to the Open Innovation paradigm, looking to Europe as a reference path.
CERR is Digital Innovation Hub Emilia-Romagna, one of the 22 Italian Digital Innovation Hub, funded by Confindustria Emilia-Romagna and the other major industry associations of Emilia-Romagna Region, and is part of the European Digital Innovation Hub recognized by the UE. CERR is a Business Innovation and Technology Transfer Center recognized by the Emilia-Romagna regional government, a node of the High Technology Network, acting as a link between companies, researchers and institutions. CERR is also part of a wider innovation ecosystem of Public-Private Partnerships on Photonics and on Flexible Electronics.
Summary of the challenge:
Description:
Selective laser melting (SLM) or powder-bed fusion (PBF) processes enable fabrication of functional metal parts with near-net-shape geometries. Possible drawbacks are lack of precision and formation of defects due to process randomness and irregularities associated with laser powder fusion. Defects can cause a 3D print to fail, and this failure results in lost time, materials and in general resources. Identifying and mitigating defects during manufacturing in the design phase takes on additional importance in large-scale, industrial AM. To address these issues, the challenge is to investigate the possibility to merge process data from machines, CAD-simulation design and HD images inside the manufacturing chamber during operations as well as physical validation via laser scanning or mechanical tests. These data can provide feedback for an in-situ control system and can be combined with the existing recognition of defects to create an AI processing descriptive\prescriptive expert system to adjust process or improve design.
An effective process system will:
- Locate defects in the processing layer
- Identify any irregularity within the 3D CAD
- Correlate the processing parameters with the defects
Data:
Data Provider:
BI-REX COMPETENCE CENTER: Process parameters and images trended over time to manage defect identification and mitigation. Provides process parameters collected from the processing log, CAD drawings of the products to be created, set of images taken during the process.
Open source:
Energy price: https://www.oecd-ilibrary.org/energy/data/end-use-prices/indices-of-energy-prices-by-sector_data-00444-en
Raw material price: https://www.oecd-ilibrary.org/economics/data/prices/producer-prices_data-00535-en
External Data Provider:
Provided by applicants
Expected outcomes:
- Optimize printing process understanding defects source and occurrences during manufacturing
- Improve process efficiency developing descriptive-predictive-prescriptive data-driven models
- Increase processes sustainability level, total cost of ownership savings
How do we apply?
Read the Guidelines for Applicants
Doubts or questions? Read more about REACH on the About Us page,
have a look at our FAQ section or drop us an email at opencall@reach-incubator.eu.