Predictive maintenance and production optimisation in industry
Application Track:
Code:
Domain:
Proposed by:
Entity Logo:
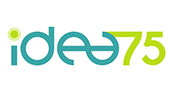
Summary of the entity:
IDEA75 provides innovative solutions for process optimization and energy efficiency of industrial plants following the new guidelines of Industry 4.0 and ISO 50001. The company has gained skills and experience in design and implementation of system automation, monitoring and supervision of production lines and automatic control systems. Idea75 has installed a smart supervisor for the energy efficiency of the flour mills for the largest European producer of semolina flour. The smart supervisor was installed in 6 production plants monitoring over 3000 devices.
Description of the global challenge:
This challenge is aimed at optimizing production. The creation of a platform that analyses and processes big data coming from the field and from automation and production management systems is able to provide operators with a predictive maintenance program, which warns of any incipient failures (avoiding unexpected failures and downtime production) and Zero-defect manufacturing to minimize the production of defects in real time (for example by correcting realtime the process to obtain characteristics that comply with the specifications).
The system will acquire a large amount of data from sensors already present in the plant. As a closed-loop system, controllers are immediately alerted to any defects, and changes can be made on the fly to eliminate the source of the problem. The approach has the potential to dramatically reduce scrap by detecting production errors instantly, eliminating the propagation of defects along the process stages. The system will also incorporate knowledge-based loops, providing information and feedback to other levels of the manufacturing chain, such as design and product development, to help minimise all failures by continuous optimisation of the production process and the manufacturing system.
Sub-challenges composing this experiment:
This challenge is composed of 2 sub-challenges:
- Monitoring and maintenance of machinery (REACH-2022-READYMADE-IDEA75_2.1)
- Production optimisation (REACH-2022-READYMADE-IDEA75_2.2)
Expected global results:
The global goal of this challenge is to increase quality and efficiency, reduce waste, boost competitiveness and lower costs for manufacturers, particularly small and medium enterprises. The expected results are:
- Reduction of unplanned stops up to 50% due to predictive maintenance.
- Reduction of production waste by 20% according to the ZDM paradigm;
- Reduction of the unsold product rate of 10% due to bad quality.
MONITORING AND MAINTENANCE OF MACHINERY
Code:
REACH-2022-READYMADE_IDEA75_2.1
Summary of the sub-challenge:
The objective is to predict incipient faults of industrial machinery to increase the overall plant availability.
Description of the challenge:
The objective of this challenge is, starting from the massive collection of data on the use of machinery, to develop analysis tools that allow the implementation of corrective maintenance actions capable of transforming unexpected stops into shorter and less frequently scheduled maintenance stops, thus increasing the overall availability of the plant.
The collection and analysis of data allows the definition of predictive models that allow to warn of plant problems and to plan maintenance activities. Training data set should be defined based on the data available, on the type of algorithm used and on the operational needs of the company. Strategy of retraining for the models used should also be investigated.
Data to be used:
Expected outcomes:
Reduction of unplanned stops up to 80% due to predictive maintenance.
PRODUCTION OPTIMISATION
Code:
REACH-2022-READYMADE_IDEA75_2.2
Summary of the sub-challenge:
The objective is to reduce scrap parts and defective products in a production line.
Description of the challenge:
European industry is required to produce high quality products at a low cost in the most efficient way to remain competitive and keep its leading manufacturing position. Today, the manufacturing industry is undergoing a substantial transformation due to the proliferation of new digital and ICT solutions, which are applied along the production process chain and are helping to make production more efficient as in the case of smart factories. The goal of this challenge is to develop and establish a digital platform for smart factories for achieving excellence in manufacturing through zero-defect processes and products thanks to the use of big data technologies and data analytics. The provided dataset could be considered as a basis to go through AI based analysis to investigate any fault or production line stop which could be related to a reduction on quality of the final product. Predicting this kind of event can be useful to warn operators of a possible waste. Dataset could also be enriched with sample data to show how the system can benefit from the correlation of different kinds of data such as production and consumption data.
Data to be used:
Expected outcomes:
- Reduction of production waste by 20% according to the ZDM paradigm;
- Reduction of the unsold product rate of 10% due to bad quality.
How do we apply?
Read the Guidelines for Applicants
Doubts or questions? Read more about REACH on the About Us page,
have a look at our FAQ section or drop us an email at opencall@reach-incubator.eu.